Production
We achieve a lot – every single day! We stay up-to-date with the latest technology and are highly motivated to explore new paths.
Our range of services does not suffer from friction at the interfaces with you. The prerequisites for meeting your expectations and wishes are provided by an already established and practiced risk and process management system, enabling the rapid development of a sustainably successful customer relationship.
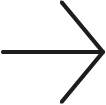
Consider our service as an integral subprocess of your existing process structure. The scope of the service and the details of the task are initially irrelevant.
Qualification through Innovation
See why our approach makes us the right fit for your project!
Milling Technology
From idea to product, from prototype to series production.
State-of-the-art machines, advanced software, and motivated, experienced employees ensure stable process flows in milling technology.
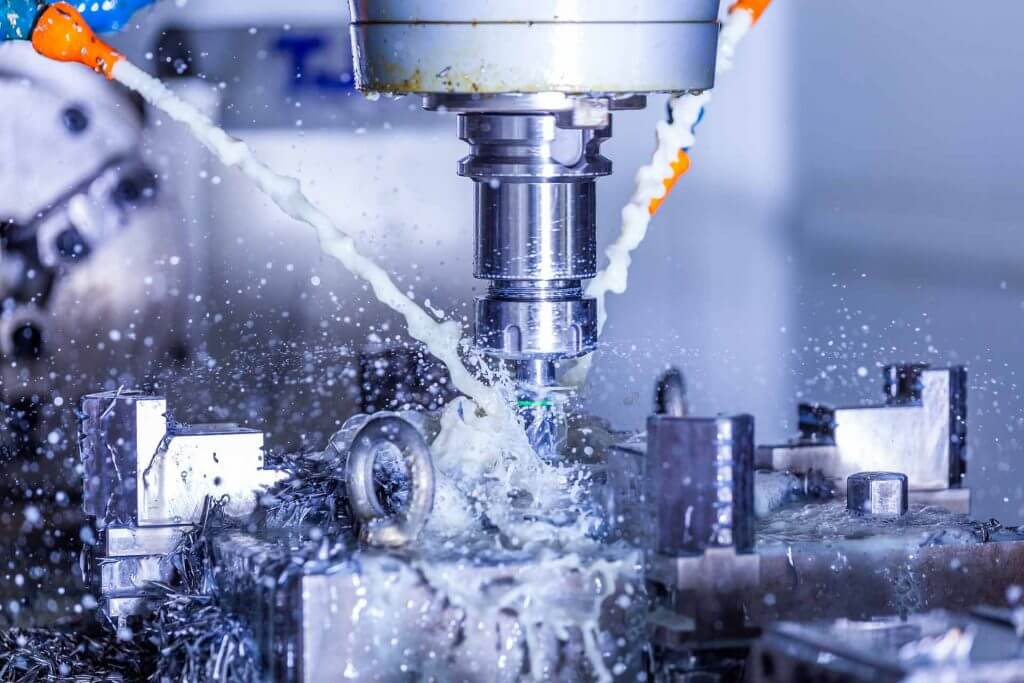
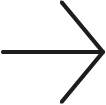
Milling technology ushered in a new chapter in the company’s history in 1982. With a young management team, an initial NC-controlled milling machine for in-house tool manufacturing, and rapidly developing computer technology, including artificial intelligence, a lasting enthusiasm for ongoing technological transformation was ignited.
Freeform surface and CNC machining in the early 1980s were the first service offerings for the local tool and mold making industry.
In the production area of CNC milling. From single parts to small, medium, and large series, the focus is on the machining of aluminum, specifically the production of thin-walled components. Our machines excel particularly with high machining volumes, complex geometries, and freeform shapes in combination with these thin-walled components. The interplay between CAM tools and machines results in effective production times with high manufacturing quality.
CNC MILLING TECHNOLOGY
High-tech in mechanics. At Forte + Wegmann, we offer you the highest technical standards in mechanical processing.
For the machining of complex workpieces and mechanical components, we have 5-axis milling centers from Grob and Matsuura at our disposal. We achieve a high degree of automation through robotic loading, and equipping the milling centers with pallets allows us to maintain highly flexible process flows. This enables us to ensure the highest process reliability and quality, even in large-scale series production.
INDUSTRIES: Aerospace, Elektronik, Automobil
MATERIALS: Aluminium, Eisen
REFERENCES: Schwarz & Rhode
Design enclosures with panel system
Take a look at the case study on our enclosure development for a customer.
5-axis milling offers a number of advantages over traditional 3-axis machining. It allows for the production of more complex parts, such as those with cross holes and undercuts, which would require multiple setups on a 3-axis machine.
Machining processes can be significantly shortened, more stable tools can be used, and better surface qualities can be achieved. Simultaneous milling occurs when the positions of the B- and C-axes for tilting the milling head are not only adjusted but also changed simultaneously during the movement of the X-, Y-, and Z-axes. This allows for the milling of freeform surfaces and cylindrically or spherically curved surfaces. Operating all five axes simultaneously typically requires significantly more effort in programming and creating complex machining strategies.
Parabolic Performance Cutting (PPC) combined with the ability to fully automate the control of the cutting edge contact point during machining enables further optimization of this highly effective milling process. Continuously adjusting the tilt of the cutter ensures even use of the cutting edge radius and expands effective milling strategies. As a result, this not only shortens manufacturing time but also ensures safer machining of the entire surface with excellent surface quality.
In true high-speed machining, it’s not just about high spindle speeds. Like in Formula 1, the engine power must also be transferred to the road or, in this case, to the workpiece – with skill and understanding.
We utilize high spindle speeds to achieve high material removal rates in aluminum machining, enabling the creation of fine wall thicknesses and achieving high surface quality without rework. Our HSC (High-Speed Cutting) machining centers offer excellent values in feed rates and rapid traverse speeds in addition to high spindle speeds. This allows us to bring true high-speed machining combined with absolute precision to the workpiece.
PROCESS SUPPORT
From prototype to series production – we always keep your product in sight and continuously check for the best quality.

Assembly
Laser marking is a precise and permanent marking process, ideal for labeling our aluminum products, whether raw, electroplated, or painted. This contactless process uses laser beams to apply detailed graphics, text, and barcodes directly onto the surface without damaging the material. The resulting marking is abrasion-resistant, heat-resistant, and waterproof, and represents an absolute criterion for traceability and batch purity. It is an integral part of our manufacturing processes for our customers.
Batch traceability is an essential requirement in the aerospace industry to uniquely identify each assembly and product that emerges from the assembly processes. By applying laser marking, permanent and precise batch numbers or barcodes are directly applied to individual parts. Standard parts are also assigned to the respective assembly with batch accuracy in the ERP system. This systematic recording and assignment increase transparency and enable efficient traceability throughout the entire production and delivery process, supporting compliance with strict industry standards and regulatory requirements.
Innovation as a Quality Feature
Learn how our innovative approach perfectly fits your project!
ARINC
ARINC short for Aeronautical Radio Incorporated, is a company based in Annapolis, Maryland, USA. Over the past years, the company has made a name for itself in the aviation and avionics sectors by standardizing numerous communication protocols between various computer systems based on ARINC’s recommendations. Additionally, the ARINC standard describes the form, fit, and function of “black box” enclosures and their installation arrangements in aircraft. The enclosures in the ARINC standard vary in size, shape, and function, but are all built to specific standard dimensions.
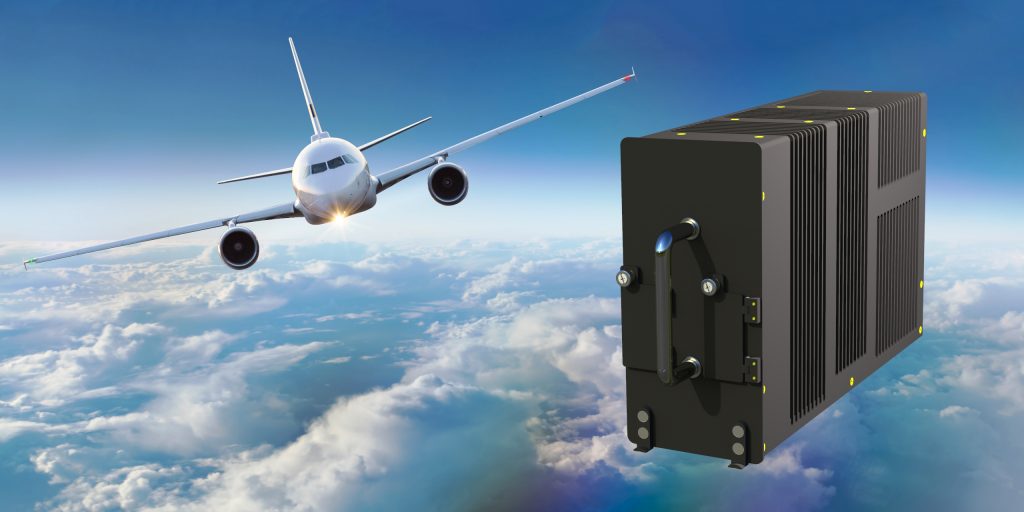
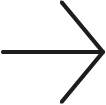
Enclosures for the aviation industry are subject to special requirements. In addition to high EMC (Electromagnetic Compatibility) properties, the enclosures must withstand extreme shock and vibration loads. In practice, customized aluminum constructions based on ARINC 404 or ARINC 600 MCU specifications have proven effective. Our experience in manufacturing this enclosure standard allows us to effectively implement your custom-designed enclosure.
Hier ist die Übersetzung:
We support you in the specific implementation of the desired design and defined requirements. Often, the front panel is modified, and the back panel is adjusted for connector cutouts. The service scope includes changes to mounting holes and adaptation to related hardware; special card and air guides, brackets, as well as specific surface finishing and laser marking.
Our philosophy has always been to economically meet these high standards for special applications, even with small batch sizes.
.